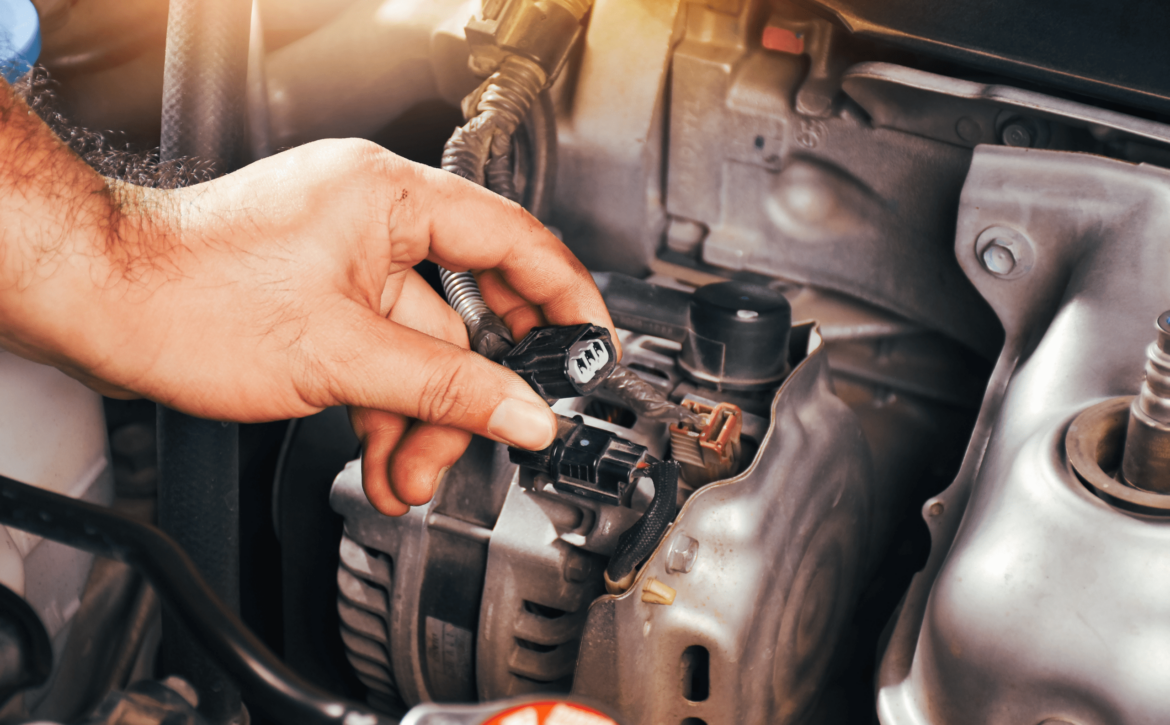
VDA 450: Vehicle Power Supply and Functional Safety – LV net voltages
This article offers an in-depth look at topics related to Functional Safety and Electric Mobility. The series continues with Part 2.
For expert-level training—including certification-based programs—on these topics and more, explore our Automotive trainings. To learn how we support product development, compliance, and organizational safety goals with consulting support, visit our Functional Safety & Cybersecurity and Electric Vehicle Development pages—or contact us directly.
1. Vehicle Power Supply System – VDA 450 Provides Clarity
If your electronic product is intended for electric vehicles (EVs), you might find that customers are often unable to provide sufficient requirements. For instance, with low voltage (LV) net voltage ranges, the VDA 450 standard can be very useful. Most of the VDA 450 standard focuses on safety-specific aspects of vehicle power systems.
Developing a new electronic product for automotive applications can be daunting, especially without clear requirements as a starting point. As you dive into the design process, countless questions arise: What is the maximum voltage I should design for? What voltage thresholds should I set for under- and overvoltage faults? What should my input capacitance be? The VDA 450 addresses the low voltage bus, whereas considerations for High Voltage (HV) safety are covered by other standards, as shown in our SRES HV Electrical Safety Training.
Beyond the classic hardware and software design, functional safety may be another critical factor. You need safety goals and safety requirements, which introduce additional system considerations, such as safety mechanisms, deciding on redundant sensors and monitoring circuits etc. Uncertainty is the enemy of functional safety, making well-defined guidelines essential.
If you’re designing electronics for EVs, you may not always have a customer-provided set of comprehensive requirements. This is where VDA 450 comes in—offering clear guidance on LV net voltage ranges to reduce ambiguity and ensure robust system design. While VDA 450 covers voltage considerations, its primary focus is on the safety aspects of vehicle power systems. In the next blog, we’ll explore these Functional Safety-specific topics in more detail.
2. Defining LV Net Voltages
In the context of power supply, VDA 450 eliminates some uncertainty by defining low-voltage (LV) net voltage ranges. While major car manufacturers establish their own LV voltage specifications, no publicly available standard or recommendation—until now—has comprehensively addressed these requirements.
Current vs. Future vehicle LV power supply systems
VDA 450 distinguishes between “current EBNs” and “future EBNs”. EBN refers to the vehicle’s electrical power supply system by abbreviating the German term Energiebordnetz (“onboard energy net”). The need for differentiation arises due to the varying energy consumption and supply behaviors between internal combustion engine (ICE) vehicles and electric vehicles (EVs).
In ICE vehicles, starting the engine demands a large surge of current, causing significant voltage drops—sometimes to as low as 4.5V or below in traditional 12V battery systems. Additionally, load dumps—voltage spikes caused by the sudden disconnection of large electrical loads or the battery—increases requirements for resilience of components against higher voltages. These events may stem from issues like poor grounding or corroded connections.
For EVs, while similar electrical phenomena still exist, their impact shifts to the traction inverter. Voltage fluctuations now primarily affect the high-voltage (HV) net. Sophisticated techniques in the traction inverter are used to counter voltage fluctuations, yet corner cases such as opening the battery contactor under high load remain a concern.
Standardized Voltage Ranges
VDA 450 defines Safety-Related (SR) LV net voltage ranges for 12V, 24V, and 48V systems. By providing standardized voltage classifications, VDA 450 removes a lot of uncertainty for suppliers of automotive electronic systems and ensures greater compatibility across different vehicle architectures.
For example, let’s say you’re developing a traction inverter for a range of EV architectures without having a large OEM (Original Equipment Manufacturer; common reference used for vehicle manufacturers) that provides LV net voltage ranges. VDA 450 helps answer design questions early such as “does the internal supply need to use a boost circuit to operate down to 4.5V?” or “what is the maximum voltage rating of electronic hardware components needed in the inverter LV net input circuit?”
The following tables reflect the technical specification of the LV net voltage ranges outlined in VDA 450.
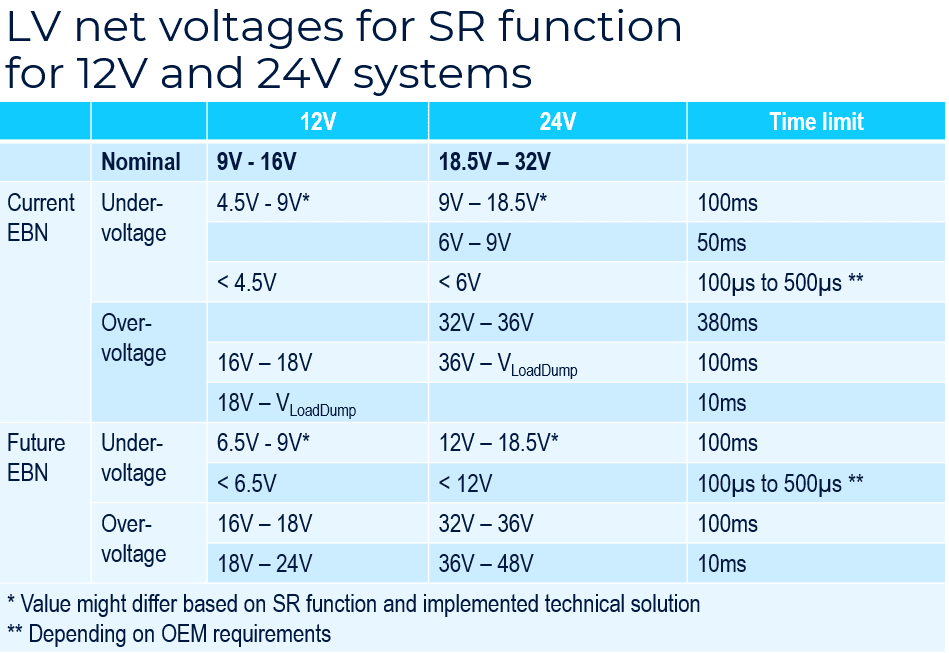
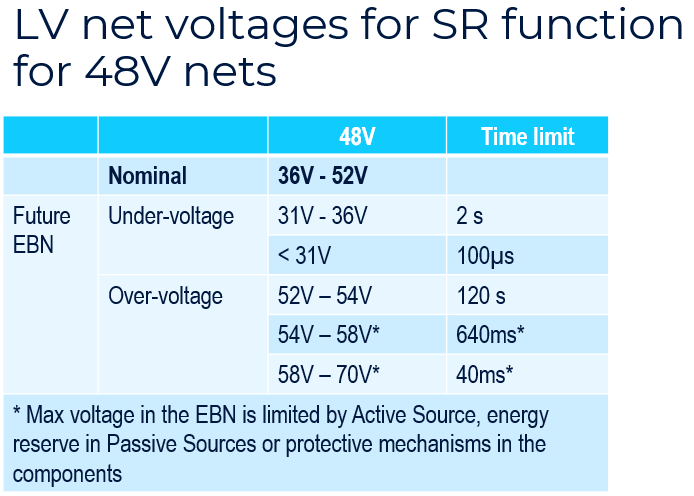
A breakdown
At first glance, these voltage ranges might seem like a lot of numbers. Let’s break them down for a better understanding.
Nominal Voltage
At the top, we see the nominal voltage ranges for 12V, 24V, and 48V systems, which are further categorized into current EBNs and future EBNs.

Voltage range differences between ICE and EVs for 12V vehicle architectures
As previously discussed, the key differences between current and future EBN are driven by the starter in ICE vehicles—which can cause voltage drops to as low as 4.5V—and the effects of load dumps (VLoadDump), which result in high voltage spikes. The markup highlights the change from the lowest undervoltage threshold of 4.5V for ICE to 6.5V for EV. The maximum overvoltage is marked by the Load dump for ICE and a fixed 24V limit for EVs.
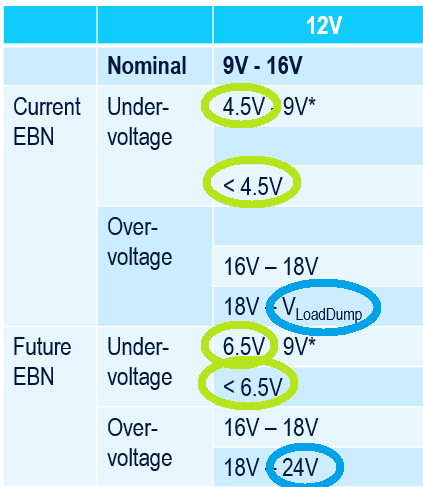
Returning to our inverter example, an internal supply circuit within the inverter would be able to stabilize a 5V output from 6.5V, eliminating the need for a boost circuit to support operation down to 4.5V—a requirement in ICE systems but unnecessary for an EV traction inverter. Furthermore, the standardized voltage limits provide clear design parameters for selecting electronic hardware components.
While these guidelines are valuable, it’s important to note that electrical test standards for EVs have yet to be fully updated. Existing voltage pulse and overvoltage tests for 12V and 24V LV nets, as defined by ISO 7637 and ISO 16750, still require supplier-specific adaptations to meet EV requirements.
Voltage range differences between ICE and EVs for 24V vehicle architectures
For 24V ICE systems, an additional undervoltage range of 6V to 9V exists. In contrast, future EBNs simplify this by using 12V as the threshold, reflecting the different power characteristics of electrified vehicle architectures.
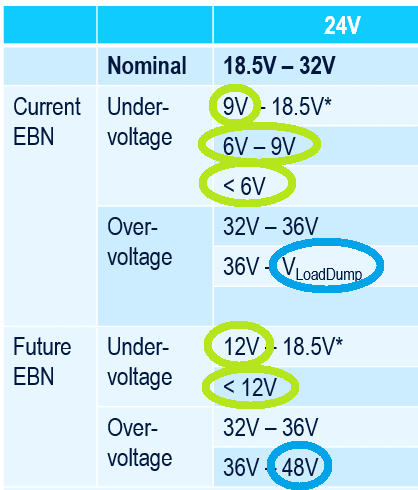
Voltage ranges for 48V vehicle architectures
The overvoltage behavior in 48V systems is primarily influenced by their energy sources. These sources can be categorized as:
- Active sources – such as generators or DC/DC converters
- Passive sources – including batteries and capacitors
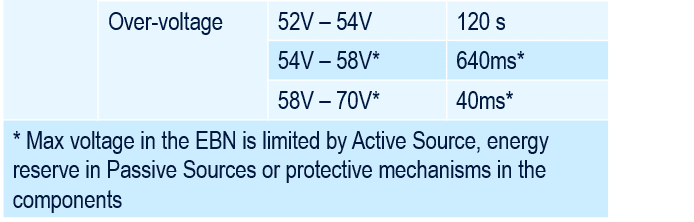
ISO 21780 provides a dedicated standard for 48V vehicle architectures, ensuring consistency in voltage regulation and safety requirements. However, 48V systems are not yet widely used for SR loads. As a result, mixed architectures—combining proven 12V systems with newly developed 48V loads—are expected to dominate in the near future.
Timings of Voltage Ranges
The time limits on voltage fluctuations are essential to account for noise and transient variations in the power supply. For instance, when a significant load is switched on or off, the voltage drop across the wiring harness can introduce fluctuations and generate switching noise.
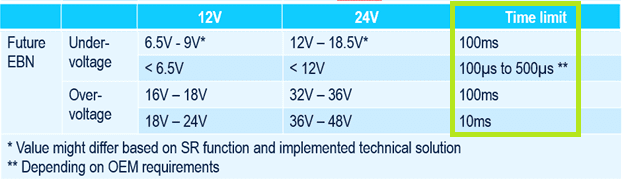
Let’s consider practical application examples of these time limits:
- The electronic supply circuit should be capable of continuous operation below 6.5V (e.g., down to 6.0V).
- A software fault configuration would trigger a fault notification if the supply voltage remained between 6.5V and 9V at the terminals for more than 100ms.
- There is some flexibility in handling voltage fluctuations in and out of undervoltage and overvoltage ranges. A well-designed averaging filter or counter mechanism can help mitigate transient effects.
The capacitance of the electronic supply circuit must be designed to sustain operation above the required time limit specified for 6.5V, accounting for tolerances and ensuring enough time for fault detection, communication, and storage. For example, a minimum time limit of 1ms before the internal supply voltage begins to taper off would be a reasonable design consideration.
Summary: The Role of VDA 450 in Vehicle Power Supply and Functional Safety
So far, we have explored two critical aspects of VDA 450:
- The Importance of the Power Supply System for Functional Safety – As vehicles transition to higher levels of automation, power distribution becomes a crucial safety factor. Traditional Fail-Passive architectures are no longer sufficient for ADAS and ADS, which require Fail-Active power systems to maintain critical functions like steering, braking, and lighting in the event of a fault.
- Removing Uncertainty with Defined LV Net Voltage Ranges – Functional safety depends on predictable power behavior. VDA 450 addresses this by standardizing LV net voltage ranges, distinguishing between current and future EBNs to accommodate the differing demands of ICE and EV power systems.
In the next blog, we will dive deeper into functional safety-specific topics. There is the challenge of classifying the LV power net as an item, system, or element. There are needed Freedom From Interference (FFI) considerations and Functional Safety Requirements (FSRs) for individual components. Stay tuned!
Quick Link: Part 2
Have insights or questions? Leave a comment below—we welcome thoughtful discussion from our technical community.
Need expert support in designing your vehicle LV net architecture or developing a comprehensive EV validation specification? SRES is here to help—contact us today!